DGA Monitors Using Gas Chromatography (GC) Measurement Methods
In Gas Chromatography (GC), a sample of gas is analyzed by first separating the molecular compounds that make up the sample, and then measuring the concentration of each compound one‐at‐a‐time. The separation is done using an inert carrier gas to flush a small volume of the sample gas through one or more gas‐separating columns. A detector at the end of the column records a signal peak as each compound exits the column at a well‐defined “retention” time that is characteristic for that compound. The concentration of each compound is determined by comparing the amplitude or integrated area of each detected peak with that obtained when a known “calibration gas” mixture is injected into the same system.
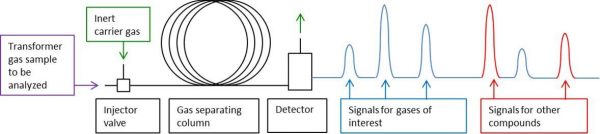
Advantages of GC methods for DGA
GC methods are the cornerstone of laboratory DGA measurements around the world. Some on‐line DGA monitors and portable DGA analyzers also use GC methods due to key advantages. The gases of interest generally used to evaluate transformer health are hydrogen (H2), carbon monoxide (CO), carbon dioxide (CO2), methane (CH4), acetylene (C2H2), ethylene (C2H4), ethane (C2H6), and the air components oxygen (O2), and nitrogen (N2).
Avoid interference from “other” species
The separate‐and‐measure approach is well suited to DGA applications because transformer liquids, and gas samples extracted from them, often contain compounds other than the gases of interest. These “other” compounds can include heavier hydrocarbon gases, alcohols, acids, SF6 (leaked into the dielectric fluid from gas insulated bushings, for example), among others. As depicted in red in Figure 1, a well‐designed GC system for DGA will separate the signals of the gases of interest from the signals of “other” compounds, so that the accuracy of the DGA measurements is not compromised by the presence of these “other” compounds.
By comparison, DGA measurements based on infrared absorption spectroscopy (including NDIR, PAS, FTIR, etc.) do not separate the gas species, but rather estimate the gas concentrations by measuring the IR absorption of a mixed‐gas sample. When the “other” compounds are present in the extracted gas sample, they can interfere with the IR measurements by causing unknown overlapping additional IR absorption in the same spectral regions used to estimate the concentrations of the gases of interest. For example, water vapor, which is present to some degree in all DGA samples, has significant IR absorption in nearly all of the spectral regions used to estimate the concentrations of the gases of interest. Interference from “other” species can lead to significant errors in the reported DGA gas concentrations, and these errors can vary unpredictably over time with negative and positive biases depending on the IR method and the algorithms used to decouple the mixed IR signals.
Calibration gas for lifetime accuracy
GC methods maintain their accuracy over the life of the product through the use of calibration gas. Nearly all gas measurement systems are prone to drift with time and with changes in the operating environment (e.g. temperature, pressure, humidity). Calibrating the GC system to a known standard on a regular basis (typically daily) serves to compensate for these drifts. As a result, gas concentration measurements in the future will have the same accuracy as those performed on their first day of use.
Another advantage of regular calibration is sometimes overlooked: The calibration results themselves are useful to verify that the gas measurement system is functioning as designed. If the calibration results are not within normal bounds, the DGA monitor can avoid reporting erroneous data which could trigger a false gas alarm condition for the transformer. Rather, the system can send a maintenance alert to the asset management team to investigate the malfunction on a non‐urgent basis.
Sensitivity
DGA monitors with low gas detection limits are advantageous for early fault detection and interpretation, particularly in new transformers. As an example, it is important to investigate the first time a new transformer develops as little as 2 ppm of acetylene, especially if this occurs early in the service life as it may indicate a manufacturing defect or transportation damage. Some monitors using GC methods have sub‐ppm detection limits for acetylene (and other gases) and are accurate in the low ppm range. This sensitivity allows such faults to be detected and tracked at their earliest onset, so that informed corrective actions may be taken to as soon as possible to minimize associated risks and damages.
Among currently available DGA monitors that use IR methods (NDIR, PAS, FTIR), none offer sub‐ppm detection limits in transformer fluids, particularly in the presence of “other” interfering compounds, and with the real‐world effects of being installed outdoors, on a transformer, and extracting gases from the oil.
Gas extraction membranes
GC methods have another advantage that is more specific to online DGA monitors. The volume of gas needed for a GC measurement is very small, generally less than 1 cm3. Such small gas samples can be extracted from the transformer fluid within a typical 1 hour measurement cycle using a semi‐permeable membrane gas extractor. Membrane extractors are effective in preventing oil droplets and vapors from entering the gas measurement system during system operation. They also provide a robust means to prevent liquid oil entering the gas measurement system during shipping and handling. In GC DGA monitors, membrane extractors keep the gas valves and gas‐separating column(s) clean, and help ensure long term performance and reliability.
Column lifetime
Most DGA laboratories use a type of GC column called a Molecular Sieve to separate some of the gases. With use, these columns gradually lose their ability to separate CH4 from N2. The degradation is caused by water vapor that is present in all DGA samples to some degree. The degradation can be partially reversed by “conditioning” the column at high temperature from time‐to‐time, but eventually the conditioning is no longer effective and the column needs to be replaced.
Experience has shown that if a Molecular Sieve column is used for DGA measurements, with 6 measurements per day, the column needs to be replaced every 3‐5 years. Some GC DGA monitors use columns that are not of the Molecular Sieve type, expressly so the columns do not need to be replaced during the lifetime of the monitor.
Maintenance costs
All DGA on‐line monitors require some amount of maintenance during their service life. Some models require scheduled on‐site maintenance to clean or change oil filters, or to ensure that external air flow paths are unobstructed. Some models require a major overhaul after 3‐5 years in service, which can be done in the field in some cases. Firmware upgrades and periodic “health check” downloads are good practice, and the associated costs can be minimized if remote communications have been configured for these tasks. Naturally, more reliable models reduce the costs associated with unplanned breakdowns.
For monitors that use GC methods, the carrier gas and calibration gas cylinders need to be replaced during the scheduled maintenance each 3‐4 years. To simplify gas cylinder management, some models remotely communicate gas pressures, gas consumption rates, and the time remaining until the cylinders need to be replaced. When comparing the lifetime cost of different DGA monitors, the cost of all service visits, materials, and repairs/overhauls should be considered.
Conclusions
DGA monitors that use GC methods are able to offer the following advantages:
- DGA accuracy is not compromised by “other” gases and compounds in the oil
- DGA accuracy is maintained throughout the product lifetime using on‐board calibration gas
- Sub‐ppm sensitivity and accuracy allowing earliest fault detection and interpretation
- Exceptional detection range from sub ppm to 100,000 ppm to cover all DGA conditions
- Membrane gas extraction to keep the gas measurement system clean and achieve long‐term reliability, and
- Some GC monitors use columns that do not require costly replacement maintenance during the monitor service lifetime.